Message
The LUCHS Register Measuring System
In all industrial printing processes, printing inks and possibly also varnishes are transferred from several printing or varnishing units to the substrate during a print run.
In each case, the precise position of the individual ink or varnish separations in the printed image is important - both in relation to each other and in relation to the substrate.
The position of the ink or varnish separations is usually set to an ideal position by the operator or by an automatic register control system during setup of the print job on the press and checked or readjusted during the print run. This process is called register setting.
During the production run, however, the individual ink or varnish separations fluctuate around their respective ideal position for reasons relating to the printing press, the material, the ambient conditions and other influences. This change in position during the production run is known as register fluctuation.
To ensure a consistently high print quality, this register fluctuation should be minimised as much as possible. However, since the position changes from print to subsequent print are stochastic, i.e. their exact amount is unpredictable, corrective intervention during the production run would not be possible even if the register shift of each individual print copy were measured inline.
Excessive register variation always leads to inconsistent print and finishing quality across the print run. In the worst case, this can affect the impression of the colour and image sharpness or, for example, a positional deviation of the type area.
With the LUCHS Register Measuring System, it is possible to analyse,
- – the positions of individual inks of a multi-colour print in relation to each other,
- – the position of the varnish (for spot varnishing) in relation to a reference ink,
- – the position of a cut or folded edge in relation to a reference ink
- – the position of a printed ink printed on the front and back side (perfecting)
over a defined number of subsequent sheets or copies with an accuracy in the µm range.
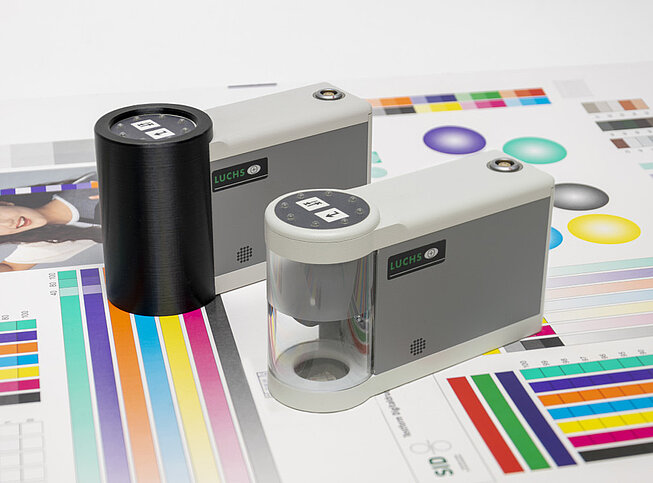
The quantitative analysis (fluctuation range, standard deviation) of these positional or rather register fluctuations over subsequent prints allows general or comparative evaluations of the printing presses, configurations or materials used.
The qualitative analysis (cyclicity of the measured values, localisation of the transfer point with the greatest register fluctuation in the printing press or the measuring position on the printed sheet, etc.) allows for an efficient readjustment of the printing press.
The fifth version of the LUCHS Register Measuring System is now available. The development of the first version began in 1994, back then with a CCD black/white camera. With the LUCHS I, the register deviations of inks printed in a maximum of five printing units could be measured lengthwise and crosswise to the printing direction in a single measurement.
Versions II and III included a CCD black/white camera and an industrial PC. Each individual measurement enabled the measurement of register deviations of up to ten colours in the lengthwise and crosswise directions. The possibility of special measurements made it possible to determine register deviations of a printed reference ink to a cut or folded edge. It was also possible to determine register deviations for front-to-back or rather perfecting printing.
With version IV, the hardware of the LUCHS Register Measuring System was offered as a single measuring head for the first time. The supplied software was installed on a separate laptop - an advantage for all those who use the measuring system in mobile applications. A USB 2.0 colour camera was used for the first time in the LUCHS IV. In terms of handling and design, the new measuring head represented a significant improvement over the somewhat cumbersome previous versions. Thanks to the new ring illumination of the field of view, the newly developed measuring elements for the colour register and the special measurement (measurement of the reference ink to the paper edge) could now be analysed regardless of the alignment of the measuring head to the measuring element. The LUCHS IV Register Measuring System enabled the measurement of up to twelve inks in the lengthwise and crosswise direction in a single measurement. Various optimised measuring elements were developed for use with different printing processes (offset, flexo and digital printing) and substrates.
Version V of the register measurement system has been available since March 2024. The new camera in the measuring head leads to a significant stabilisation of the image data flow. The new, very precise macro lens enables a very sharp, almost distortion-free image. The software-supported optimisation of the ring illumination results in a levelling of the brightness distribution in the field of view. The audible signal of the measuring head has been accompanied by a vibration signal, which ensures that a single measurement is recognised even in the presence of noisy printing presses.
In addition to the field of view illumination with white light, the LUCHS V measuring head is also available with UV light as an option. With a special varnish register measuring element, this configuration makes it possible to determine the register deviation of an image-printed varnish (spot varnish) to a reference ink printed in a printing unit. Already developed for the LUCHS IV, the varnish register option has now been integrated into the LUCHS V measuring head.
Like the previous versions, the new LUCHS V Register Measuring System has also undergone certified EMC and safety testing by SLG Prüf- und Zertifizierungs GmbH.